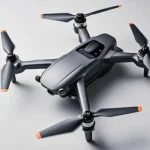
Casos de Usinagem do Veículo Aéreo NÃO Tripulado (VANT) Todo HXC
2025-03-20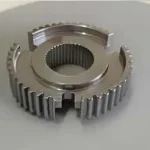
Processo de desburo e grinding do hub do sincronizador de transmissão automotiva
2025-03-21Casos de Otimização por Acoplamento CAESES e FLOW-3D: Otimização do Modelo de Moldeagem por Pressão
A moldeagem por pressão é um processo de fusão de metais no qual o metal fundido é forçado dentro de uma cavidade de molde para gerar um modelo correspondente. Neste estudo de caso, o foco é a otimização de forma de peças moldeadas por pressão. Um modelo paramétrico foi criado no software CAESES usando 8 variáveis de projeto, e os parâmetros de destino definidos foram calculados e monitorados em conjunto com o software FLOW-3D.
O principal objetivo deste estudo foi reduzir a quantidade de ar embebido no processo de moldeagem por pressão. Ao mesmo tempo, a concentração de defeitos na superfície livre (essas impurezas de superfície são principalmente óxidos na superfície livre) foi controlada para não ultrapassar o modelo de base. Um fluxo de trabalho totalmente automatizado baseado em CAESES e FLOW-3D foi estabelecido, onde estratégias de otimização do CAESES foram usadas para gerar e analisar diferentes variantes de projeto.
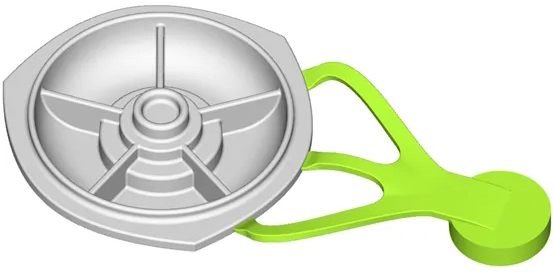
Sistema de moldeagem em que a peça verde pode sofrer modificações de forma durante o processo de otimização
Modelo Geométrico
O modelo geométrico de referência inicial é importado de fora e reconstruído em um modelo geométrico totalmente paramétrico no CAESES. As áreas do molde, canais de corrida e manga de injeção são removidas de um modelo sólido para formar um modelo de domínio fluido fechado, e um fluxo de trabalho automatizado é estabelecido para gerar automaticamente a malha.
O comprimento, ângulo e outras características geométricas da peça podem ser alterados. A animação a seguir mostra algumas mudanças típicas no modelo geométrico durante a otimização automática:
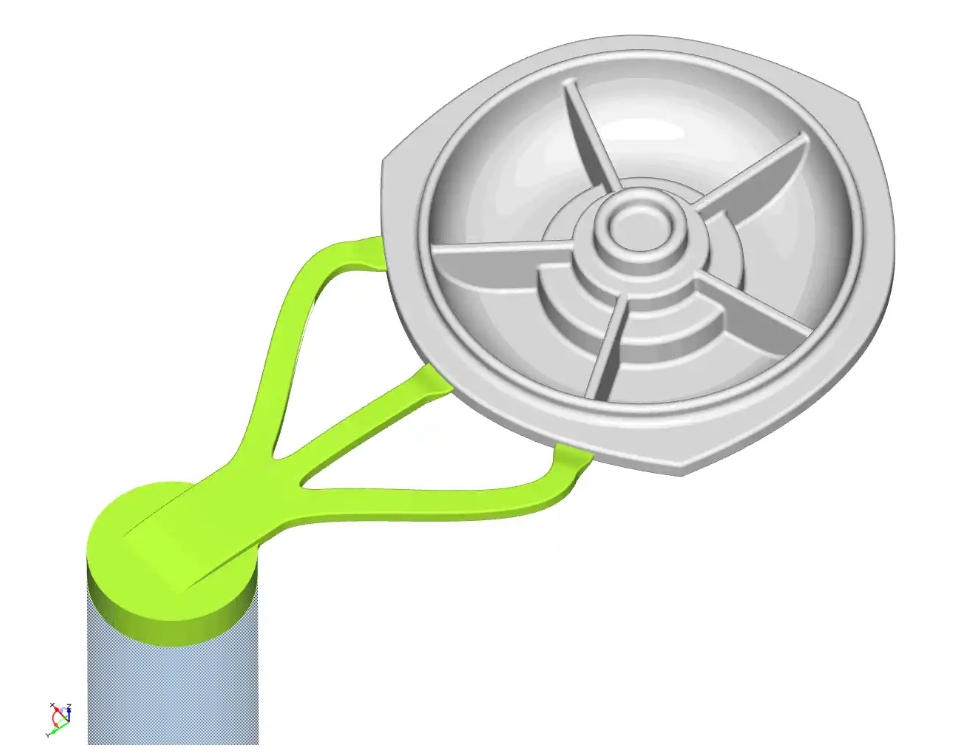
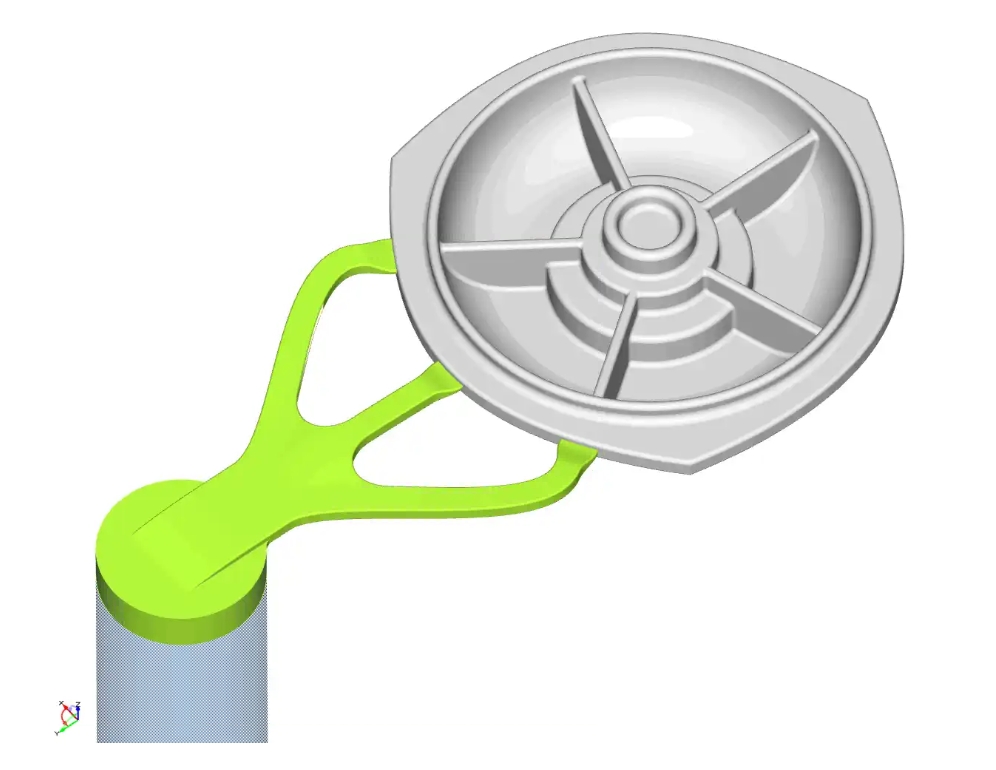
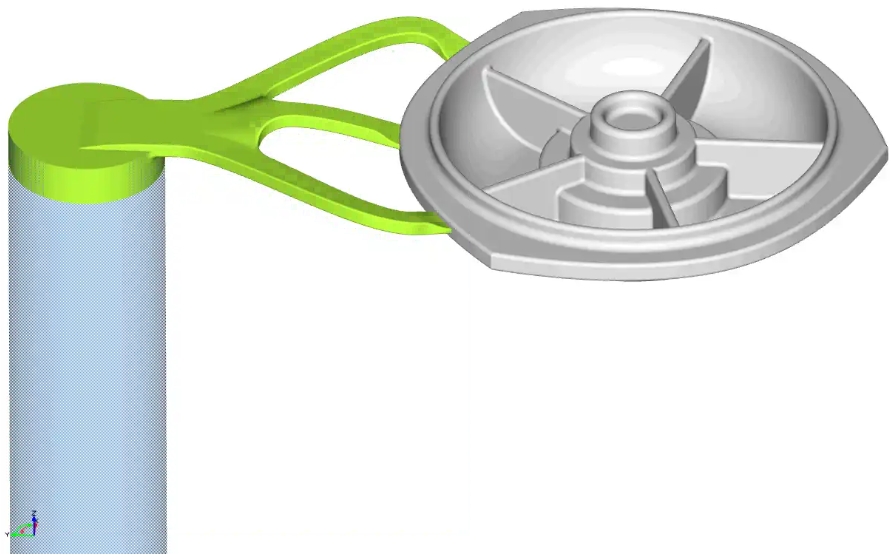
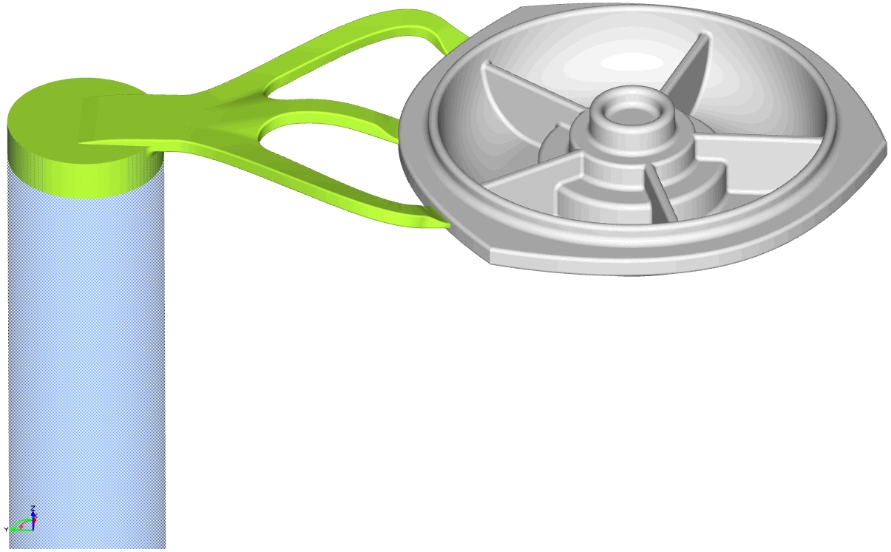
Restrições
A velocidade do líquido de moldeagem a pressão entrando no molde a partir do canal de descarga varia de 20 a 60 m/s; este modelo de seção deve ser capaz de se adaptar ao modelo inteiro do canal de descarga; quando o líquido de moldeagem a pressão entra no molde, pode entrar na fase de enchimento rápido; o fluxo do líquido de moldeagem a pressão deve percorrer o caminho mais curto da seção fina para a seção grossa.
Cálculo automático de CFD
Para o modelo inicial, as configurações de análise são feitas no software FLOW-3D, e depois essas configurações podem ser reutilizadas para as variantes novas geradas por meio da função "link de software" no CAESES. Tudo, desde as propriedades do material até os parâmetros da malha, pode ser controlado no CAESES. Os dados de resultado gerados pelo FLOW-3D podem ser importados automaticamente para o CAESES e os parâmetros de destino podem ser extraídos para avaliar os resultados da simulação.
Características da malha
O mallado do modelo inteiro consiste em duas partes de mallados não completamente combinados; o número total real de mallados é de aproximadamente 1.400.000 e o tamanho básico do mallado é de 2 mm.
Características da simulação
Para o pistão, seu material é ligas de cobre bário-cobalto (moldura de cobre), a condutividade térmica é de 300 (W/(m·K)) e a capacidade calorífica específica é de 3,52e+06 (J/(m³·K)). Para o espaço do molde, seu material é aço ferro H13, a condutividade térmica é de 28,6 (W/(m·K)), a capacidade calorífica específica é de 35.618,014 (J/(m³·K)) e a profundidade máxima de penetração térmica é de 14 mm.
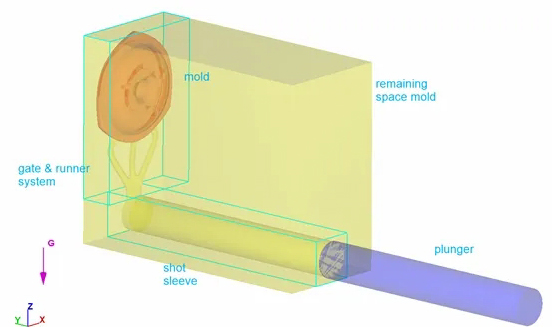
Configuração geral de cada componente da moldeagem a pressão
As características do líquido de moldeagem a pressão são mostradas na tabela a seguir:
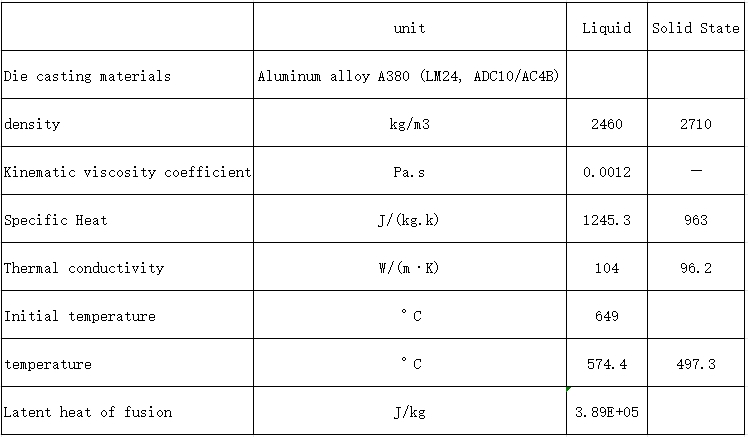
Utilize um fluido com modelo de superfície livre e aplique os seguintes modelos:
• Entrada de ar
• Cavitação
• Rastreamento de defeitos
• Avaliação de densidade
• Gravidade e referenciais não inerciais
• Transferência de calor
• Objetos em movimento e deformação simples
• Solidificação
• Viscosidade e turbulência
Resultados da simulação
O processo de otimização é dividido em duas etapas. Na primeira etapa, os parâmetros de fluxo básicos são otimizados. Na fase de enchimento rápido, a velocidade é controlada entre 1,5~2,5 m/s (o benchmark é de 1,6 m/s). Ao mesmo tempo, a temperatura do líquido de moldeagem a pressão varia entre 620°C~680°C (o benchmark é de 649°C).
Após essa etapa de otimização, a segunda etapa de simulação é realizada. Nesta etapa, as mudanças de parâmetros de forma são controladas pelo algoritmo de otimização automática.
Os resultados gerais da otimização mostram que a quantidade de ar embebido foi reduzida em 15% em comparação com o projeto baseline inicial; ao mesmo tempo, o grau de defeitos na superfície livre foi reduzido em 1%. É importante destacar que o grau de defeitos na superfície livre não era um dos parâmetros-alvo dessa otimização. As figuras a seguir mostram alguns dos resultados deste estudo:
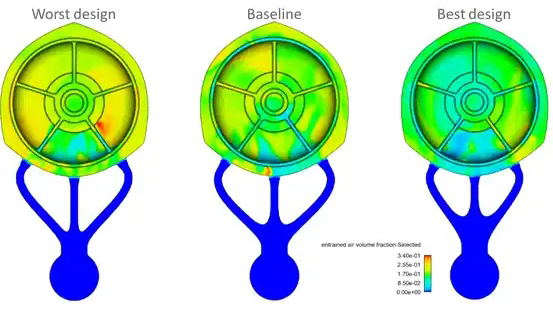
Comparação do volume de ar embebido
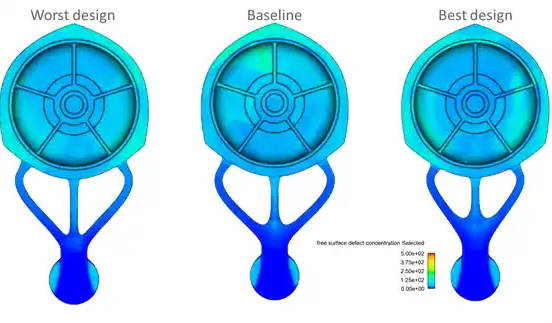
Comparação dos níveis de defeitos na superfície livre