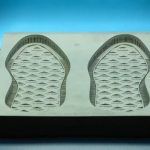
突破3D打印EVA鞋模的硬件瓶颈
2025-04-25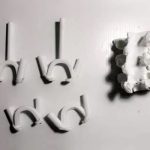
3D打印外科医疗应用案例
2025-04-25HXC公司讨论如何减薄硅胶制品?
在硅胶制品的生产过程中,有时很难将其变薄,这不仅影响产品的外观和质量,还可能导致生产效率降低和成本增加。为了进一步探究硅胶制品为什么不能压薄,我们需要从硅胶制品的生产工艺、模具设计、排气系统、模具结构、人体操作等多个方面进行综合分析。
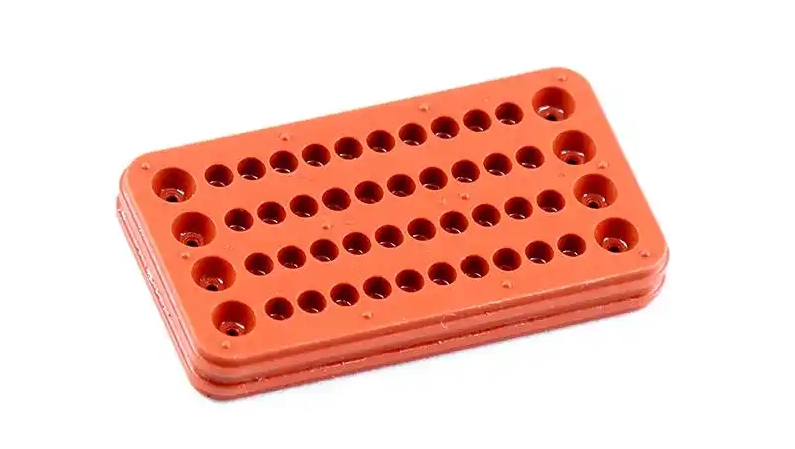
硅胶制品的生产过程对其厚度控制有着至关重要的影响。硅胶制品的成型工艺主要包括压缩成型、注塑成型(注射成型)、挤出成型、轧制、浇注和涂层。其中,压缩成型是最常用的工艺,它涉及将混合的硅胶原料放入模具中,并在加热和加压条件下硫化。
在这个过程中,温度、压力和硫化时间的控制至关重要。如果温度不够高或压力不够高,硅胶原料可能无法完全硫化,导致厚度不均匀或产品难以变薄。此外,如果硫化时间不足,还可能导致硅胶产品内部存在未固化的部分,从而影响其整体性能和厚度控制。
注塑成型是一种高精度的硅胶制品生产工艺。它是通过在加热和冷却条件下将硅胶原料注入模具中而形成的。该工艺要求模具的高精度和注塑机的性能,但一旦控制得当,可以生产出厚度均匀、尺寸精度高的硅胶制品。但是,如果模具设计不合理或注塑机参数设置不当,也可能使硅胶产品难以变薄。
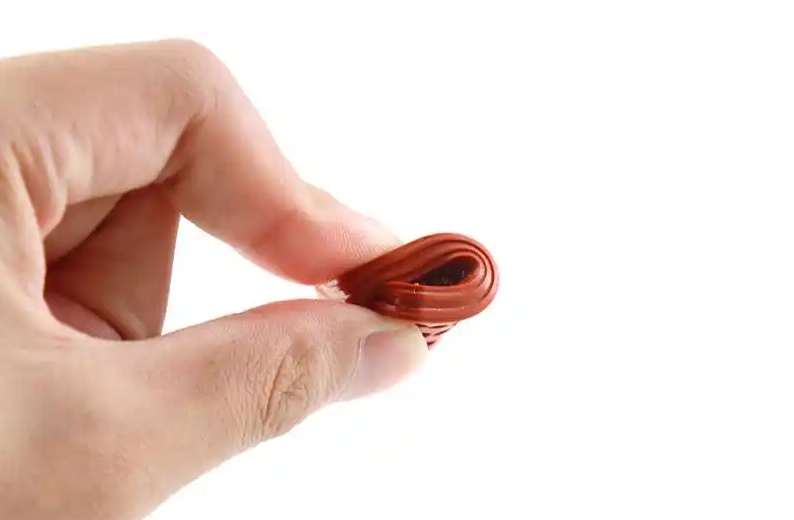
除了生产工艺,模具设计也是影响硅胶制品厚度控制的重要因素。模具的设计不仅决定了硅胶制品的形状和尺寸,还直接影响其厚度和成型效果。如果模具设计太大或结构复杂,可能会导致硅胶原料在模具中流动不良或填充不均匀,从而影响产品的厚度控制。此外,模具的精度和制造质量直接影响硅胶制品的成型效果和厚度均匀性。
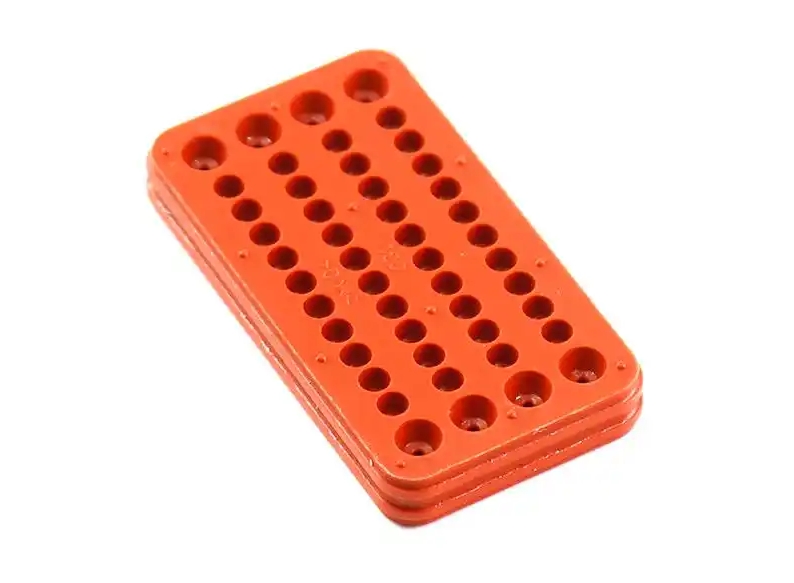
排气系统的缺失或不合理也是硅胶制品难以减薄的重要原因。在硅胶制品的成型过程中,如果模具内的气体不能及时排出,可能会导致产品内部出现气泡或缺陷,从而影响其厚度控制和整体性能。因此,在模具设计中,有必要充分考虑排气系统的设置和合理性,以确保硅胶原料能够完全填充模具并顺利排出气体。
模具结构的复杂性也是影响硅胶制品厚度控制的一个因素。对于结构复杂的硅胶产品,成型过程可能需要多个模具或步骤才能完成。这不仅增加了生产成本和工艺难度,还可能导致产品在成型过程中变形或厚度不均匀等问题。因此,在模具设计中,要充分考虑产品的结构和成型要求,以简化模具结构,提高成型效率。
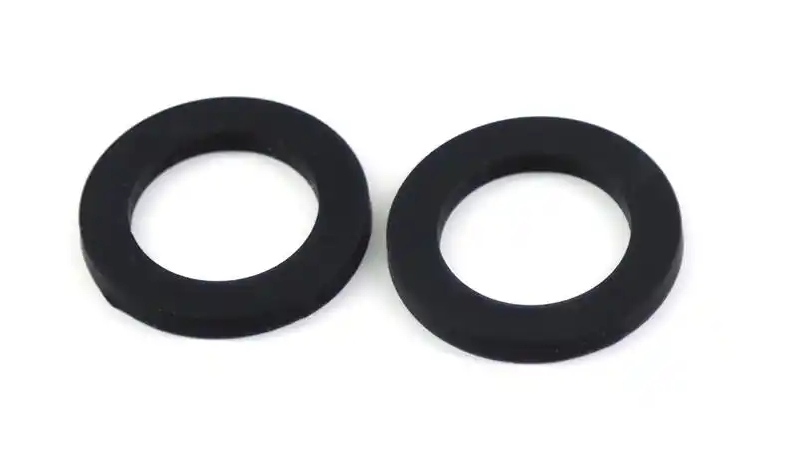
人为操作也是影响硅胶制品厚度控制的重要因素。在生产过程中,操作人员的技能水平、操作习惯和质量意识将直接影响产品的成型效果和厚度控制。例如,在压缩成型过程中,如果操作员对温度、压力和硫化时间的控制不够准确或稳定,可能会导致产品厚度不均匀或难以变薄。因此,加强对操作人员的培训和技能提升,对于提高硅胶制品的厚度控制水平具有重要意义。
硅胶制品在生产过程中难以变薄的原因是多方面的,包括生产技术、模具设计、排气系统、模具结构和人为操作。要解决这个问题,我们需要从多个方面入手,如加强生产过程的优化和控制,提高模具设计的准确性和制造质量,完善排气系统的设置和合理性,简化模具结构,提高成型效率,加强对操作人员的培训和技能提高。只有这样,我们才能生产出厚度均匀、质量稳定的硅胶产品,满足市场需求和客户期望。
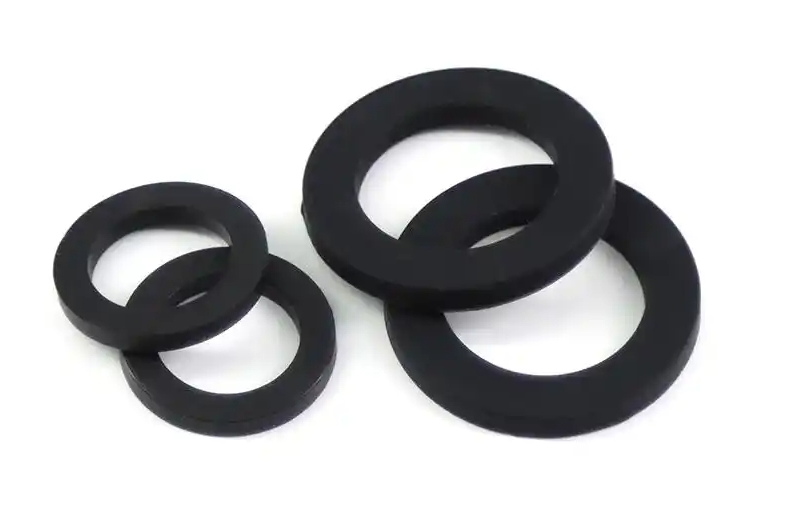
在实际生产过程中,我们可以通过优化生产工艺参数,如提高硫化温度、增加硫化压力、延长硫化时间等,进一步提高硅胶制品的厚度控制水平;二是加强模具设计和制造质量控制的精度,确保模具的精度和制造质量满足生产要求;三是改进排气系统的设置和合理性,确保模具内的气体能够及时排出;四是简化模具结构,提高成型效率,降低生产成本和工艺难度;五是加强操作人员的培训和技能提升,提高操作水平和质量意识。通过实施这些措施,我们可以进一步提高硅胶产品的厚度控制水平,为市场提供更高质量、更稳定的产品。