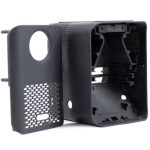
Пластиковая оболочка для аудиоустройства, напечатанная с использованием 3D-печати
2025-05-09Конструирование формы для диек스плуатации алюминиевых сплавов для переменной оболочки автомобиля
Части для диекстака переменной оболочки (с изменением толщины оболочки) — это компоненты высокого качества с сложной конструкцией, с большими различиями в толщине стенок и требуют тестирования на герметичность под высоким давлением. Поэтому необходимо избежать дефектов, такие как холодные с_joinки и пузырьки от сжатия газа, вызывающие утечки во время диекстака, или перенести их в разрешенные места.
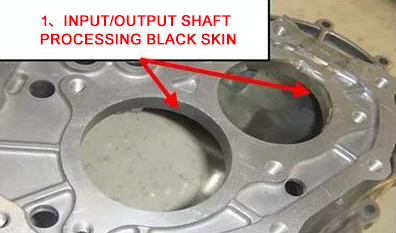
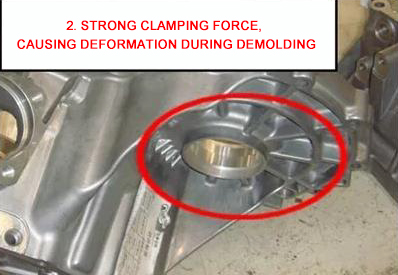
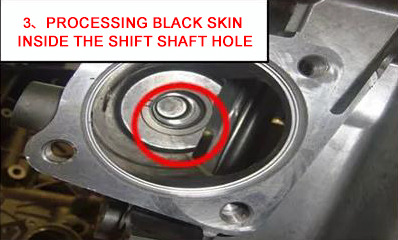
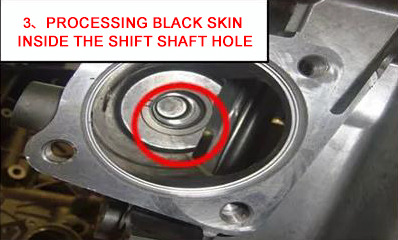
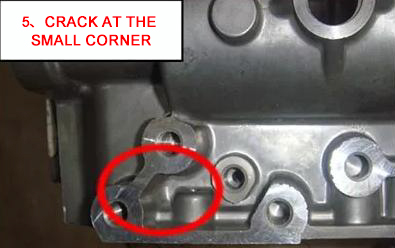
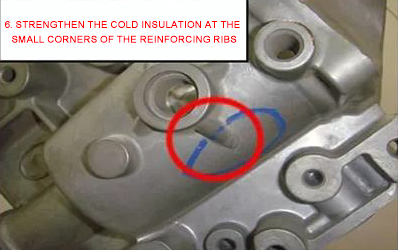
Рисунок 1 Общие дефекты при диекстаке
На рисунке 1 показаны распространенные дефекты в деталях, полученных методом диекстака. Здесь рисунки 1 и 2 относятся к проблеме припусков на механическую обработку, которые могут быть решены путем увеличения локального припуска на обработку отливки. Добавление структуры выталкивателя на стороне стационарной формы (рисунок 2) может решить проблему дефектов. Основной акцент делается на анализе дефектов отливки на рисунках 3, 4 и 5, а также на мерах по улучшению формы для диекстака.
Анализ исходной конструкции формы
На рис. 2 (а) показано расположение деталей для диекстака переменной оболочки в исходной форме, при этом расплавка заливается с одной стороны формируемой детали. Из рис. 2 (а) видно, что расплавка должна пройти через выпуклый lõкостruct с высотой 175 мм для заполнения противоположной стороны пор型腔. Геометрическая форма противоположной стороны пор型腔 относительно сложна, есть много островов для диекстака и зон невидимости. Когда расплавка проходит через зону выпуклого lõкострукт с большим расстоянием и значительным падением, уходит давление при диекстаке, и сложно обеспечить плотность внутри формируемой детали в сложной зоне пор型腔.
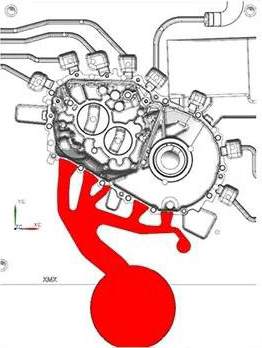
(a) Расположение диекTYлинговых деталей в исходном форм
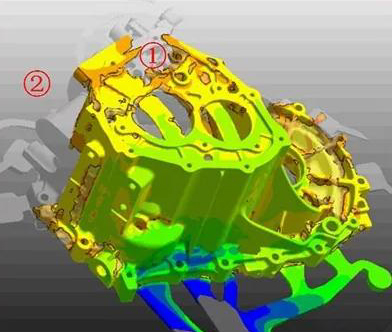
(b) Неполностью заполненный
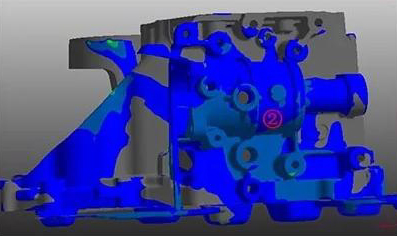
(c) Плохая плотность
Рисунок 2: Расположение литья под давлением в исходной форме и дефекты сформированных деталей
При изучении зоны ① на рисунке 2 (b) и зоны ② на рисунке 2 (c) выявлено наличие проблем с неполным заполнением и низкой плотностью. Для решения этой проблемы необходимо добавить питательный канал в нижней зоне, противоположной формируемой детали диекTYлинга, для компенсации потери давления фронта расплавленного материала. Если вносить изменения только в исходный вариант формы, то добавленный浇口 (вводящий канал) окажется слишком длинным, что приведет к слишком высокой потере давления и большому количеству отходов. Поэтому после изучения и перепроектирования новых форм можно полностью устранить вышеупомянутые дефекты.
Оптимизированный дизайн схемылияния
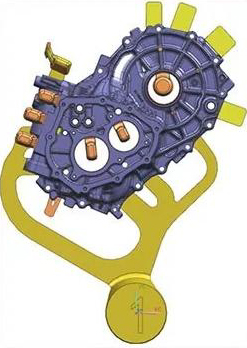
(a) Оптимизированная схема заливки
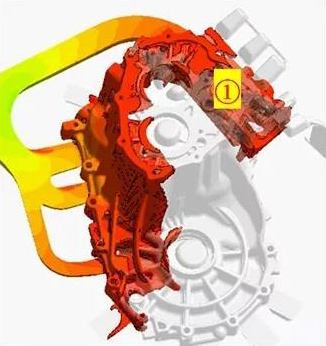
(b) Симуляция заливки при 20%-ном заполнении отливки
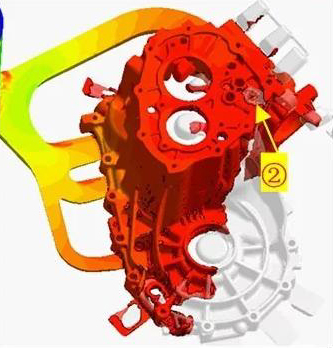
(c) Симуляция заливки при 80%-ном заполнении отливки
Рисунок 3 Оптимизированная схема заливки и CAE-симуляция литейного процесса
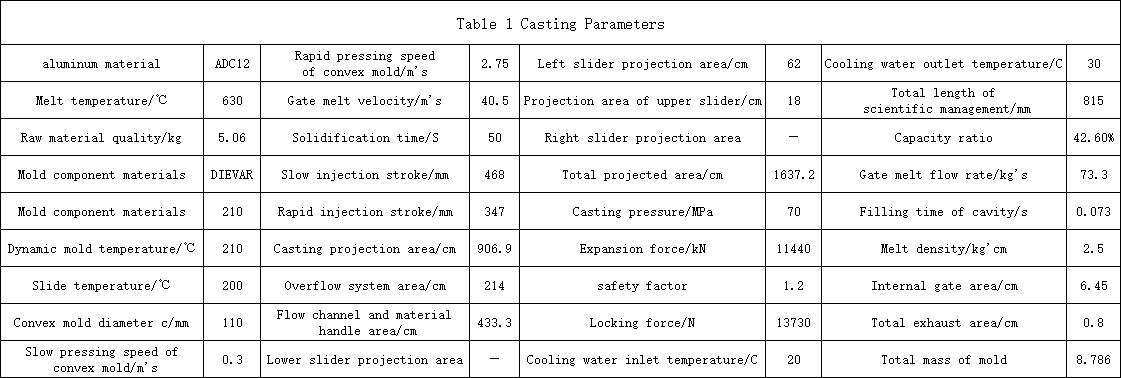
Эта схема заливки позволяет решить дефекты литинга исходной формы и достичь идеального состояния. Оптимизированные параметры литейного_processа в форме приведены в таблице 1.
Оптимизированная конструкция литейной формы
Динамическая конструкция формы показана на рисунке 4
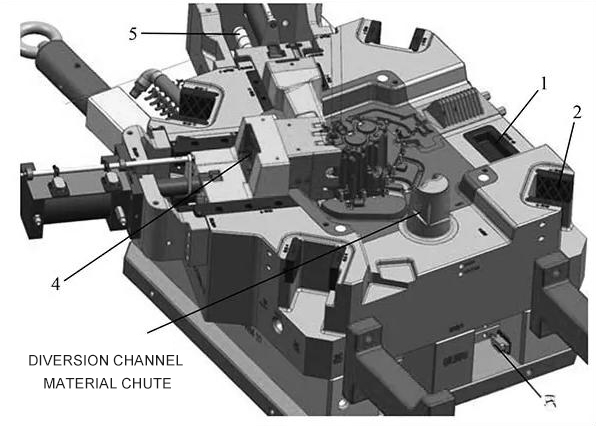
Рисунок 4 Динамическая конструкция формы
1、Позиционирующий блок
2、Трение-образующий блок квадратного направляющего стержня
3、Концевой выключатель ограничения хода верхней плиты
4、Прессовая плита для быстрого изменения сердечника
5、Направляющий стержень ползуна
Трение-образующий блок квадратного направляющего стержня
Большие диекTYлингие формы (размеры рамы формы 1500–2000 мм) сильно受制于 termalного расширения. При температуре рамы формы в 100 °С осьевое расширение составляет 0,12 мм. Из-за конструкции и других факторов фактические данные составляют около 0,2 мм. Одновременно.circularная форма отверстия в направляющем цилиндре может привести к накоплению тепла, которое не может сброситься, в итоге ведет к локальному过得配合 направляющего цилиндра и втулки, что вызывает невозможность раскрытия формы. Использование конструкции с квадратным направляющим столбцом позволяет эффективно избежать вышеупомянутых проблем.
Отводящий канал (материальный шute)
Разводящий канал оснащен вертикальной канавкой размером 5×5 мм, которая использует силу трения, создаваемую ненаклонным прямым ребром, для воздействия на отливной крючок и затвердевший стержень литника. Это предотвращает риск задержки крючка и затвердевшего стержня на стороне неподвижной формы при открытии формы и обеспечивает беспрепятственное извлечение отливки при разборе формы.
03. Прессовая плита для быстрого изменения сердечника
На задней стороне штока сердечника выполнена цельная зажимная плита, которая крепится к соединительному блоку ползуна. В случае необходимости замены сердечника в процессе литья под давлением все сердечники могут быть заменены путём демонтажа этой плиты прямо на машине для литья под давлением, что позволяет избежать разборки ползуна и сократить время простоя оборудования.
Направляющий столбец ползуна
Ползун на форме имеет ход вытягивания 200 мм. Использование конструкции с направляющим столбцом обеспечивает более плавное движение ползуна во время вытягивания, đồngzeit снижает вес формы и энергопотребление.
Позиционирующий блок
Форма не имеет правого ползуна. Для компенсации односторонней силы левого ползуна на правой стороне рамы формы разработана грубая позиционирующая конструкция.Динамическая позиционировка формы в основном dựевается на тонкой позиционирующей конструкции на сердечнике, чтобы избежать повторной позиционировки.
Концевой выключатель ограничения хода верхней плиты
Для защиты толкателя под ползуном, помимо существующей штоки сброса, добавлены верхний выключатель ограничителя и точка срабатывания, обеспечивающие безопасность.
Неподвижная конструкция формы 2
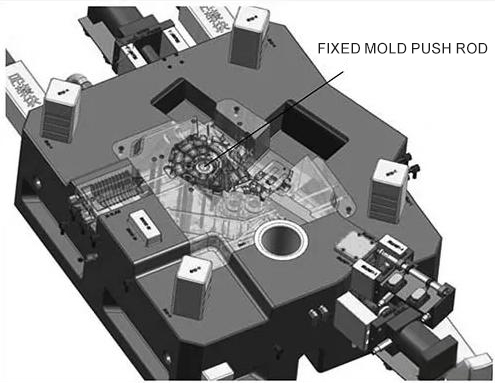
Рисунок 5 Неподвижная конструкция формы
На рисунке 5 показана неподвижная конструкция формы. Для преодоления дополнительного压紧ющего усилия неподвижной формы, возникающего при формировании деталей сложной формы, разработана mehанизм выталкивания с стороны неподвижной формы, включающий плунжер неподвижной формы, направляющий стержень, втулку направляющую, шток сброса и другие конструкции.
Система обработки и онлайн-измерений
3. В результате длительных исследований и экспериментов текущая схема конфигурации систем инструментов для высокоскоростной обработки предусматривает использование высокоточных обратно-подтягивающих держателей инструмента с динамическим балансом G2.5 в диапазоне закрепления инструмента от ϕ 12 до ϕ 4 мм, с погрешностью вращения инструмента 0,005–0,008 мм, что позволяет обеспечить высокоточную обработку обычных глубин при частоте вращения до 18000 об/мин; для специальной обработки глубоких полостей применяется схема с термонасаживаемым держателем, которая обеспечивает обработку глубоких полостей малого диаметра при 18000 об/мин; цельные тунгstenовые антивибрационные держатели диаметром от ϕ 16 до ϕ 32 мм используют высокоточные высокоскоростные и мощные механизмы зажима, что позволяет достичь точных параметров обработки при частотах ниже 6000 об/мин; данное решение представляет собой в настоящее время наиболее экономичную схему подбора инструмента, удовлетворяющую требованиям высокой точности, демонстрирующую преимущество по соотношению цена–качество и имеющую высокую практическую ценность для распространения.
4. Применение технологии онлайн-измерений. После завершения высокоскоростной точной обработки сердечника программа автоматически вызывает систему зонда из инструментального склада для автоматического контроля обработанной детали в соответствии с допусками программы. Только после достижения заданных допусков деталь может быть снята с обработочного станка и передана на следующий этап технологического процесса. Это обеспечивает качество «годовки с первого раза», исключает повторные переделки и переустановки, а также экономит время на тестирование.