Обработка деталей из нержавеющей стали с использованием ЧПУ - комплексный (one-stop) сервис
ЧПУ-обработка нержавеющей стали
Благодаря особым свойствам нержавеющей стали, таким как коррозионная и износостойкость, она стала одним из материалов, часто выбираемых инженерами.
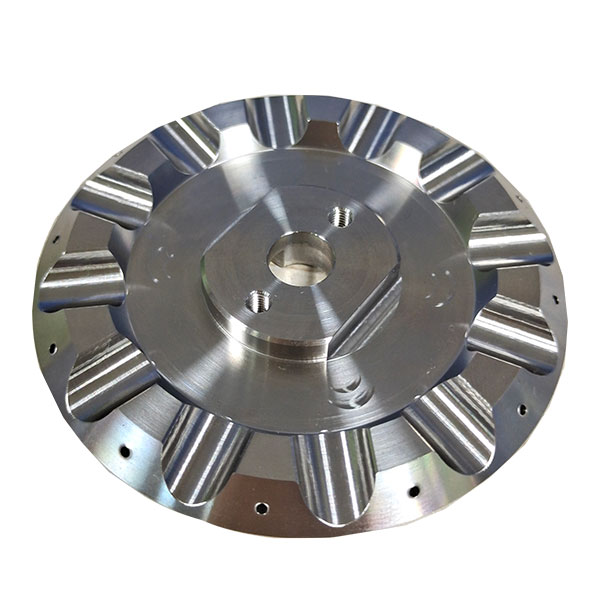
Распространенные марки нержавеющей стали: аустенитная, мартенситная, 304, 303, 316, 420, дуплексная нержавеющая сталь и др. Физические свойства различных типов нержавейки различаются. Если вашему продукту нужна немагнитность, высокая пластичность и вязкость, но не важна прочность, рекомендуется использовать аустенитную нержавеющую сталь. Если речь идет о пищевых продуктах, лучше выбрать сталь 316. Компания HXC имеет более десятилетний опыт в сфере ЧПУ-обработки нержавейки. Если вы еще не определились с выбором материала, обращайтесь к нашим онлайн-техническим инженерам.
Каковы technological процессы для ЧПУ-обработки деталей из нержавеющей стали?
Нержавеющая сталь имеет высокую плотность, твердость и отсутствует магнитная восприимчивость. В технологичном процессе фиксация и выбор инструмента отличаются от других материалов. Общими технологиями ЧПУ-обработки деталей из нержавеющей стали являются: обработка ЧПУ-фрезами, ЧПУ- tornaми, шлифовальная обработка, проволочная резка, электроды放电加工 (электроэрозия), глубокое сверление. Существует множество новых и точных технологий, а инженеры способны комбинировать различные процессы, чтобы предложить вам идеальный продукт.
Показ деталей из нержавеющей стали
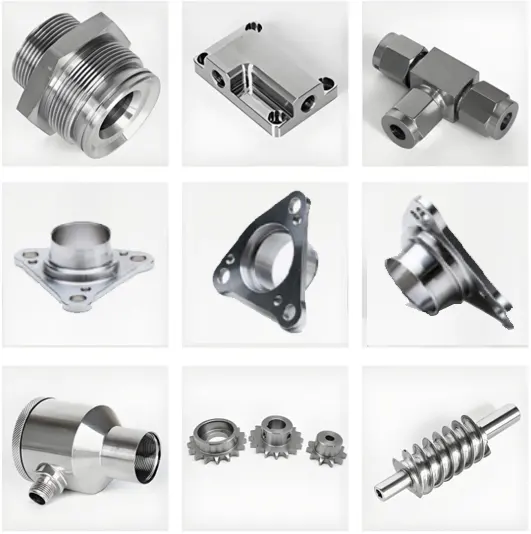
Какие поверхности обработки применяются при ЧПУ-обработке нержавеющей стали?
Обычно мы думаем, что нержавеющая сталь не окисляется и не ржавеет, поэтому нет необходимости в какой-либо поверхностной обработке. Это ошибка. Нержавеющая сталь в определенных условиях все же окисляется и корродирует, но процесс идет медленнее, чем у других сталей.
Для защиты продукции от окисления и коррозии, а также для увеличения ее срока службы и улучшения идентификации, мы длительное время предоставляем клиентам комплексные услуги по обработке и поверхностной обработке. После ЧПУ-обработки нержавеющей стали обычно применяют следующие виды поверхностной обработки: шлифование, полировка, пескоструйная обработка, порошковое покрытие, протяжка, электроникелирование, лазерная гравировка и т. д.
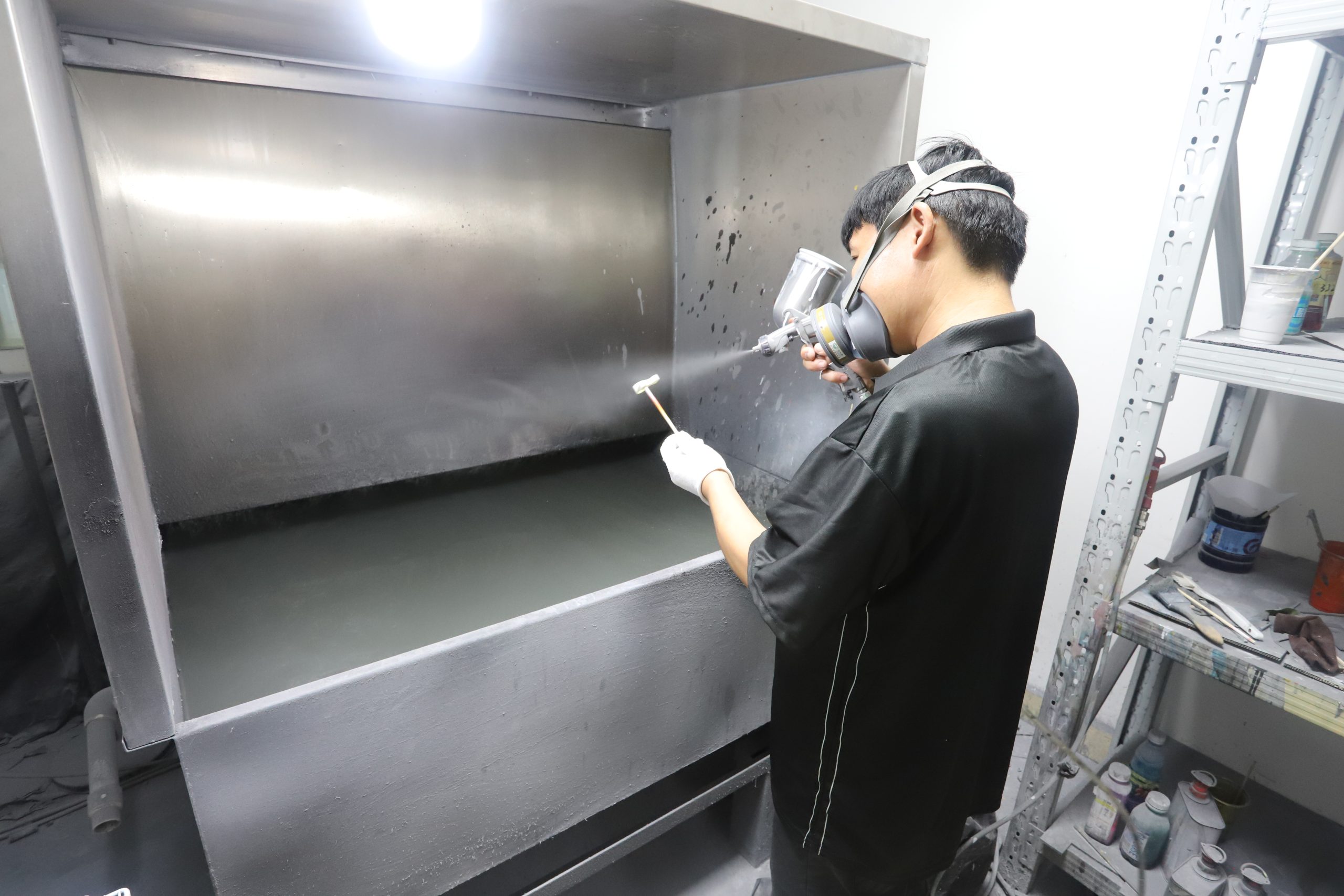
Стандарты и 절절уры контроля
1:Разработать план контроля в соответствии с применением деталей и отраслевыми стандартами (например, ASTM, ISO, GB и др.).
2:Отборочный контроль: Для серийно произведенных деталей проводить отборку в соответствии с определенным коэффициентом, чтобы обеспечить стабильность общего качества.
3::Регистрация и отслеживаемость: Сохранять данные контроля для обеспечения qualité-отслеживаемости деталей.
4:Для изделий, к качеству которых предъявляются жесткие требования, применяем метод komplexного контроля.
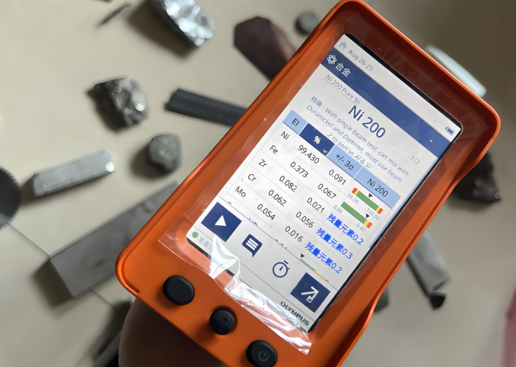
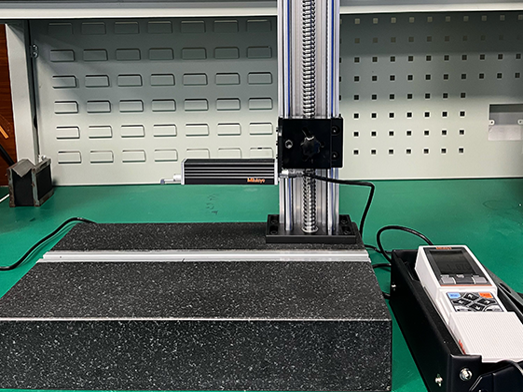
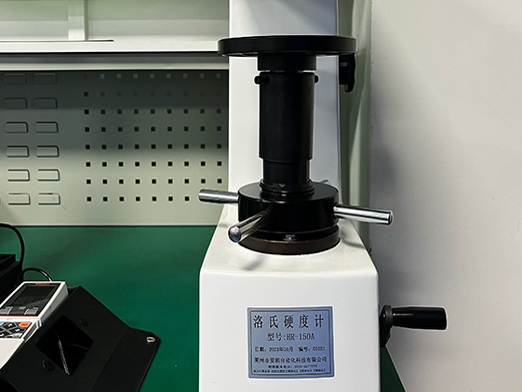
1.Контроль размеров и геометрической точности
Инструменты: Координатный измерительный Прибор (КИП), калибр, микрометр, проектор, профилометр и т. д.
Контролируемые Показатели:
Измерять ключевые размеры деталей, такие как длина, диаметр, диаметр отверстия, толщина стенки и т. д.
Проверять геометрические допуски, такие как прямолинейность, плоскость, круглость, перпендикулярность, коаксиальность и т. д.
Проверять геометрическую точность сложных криволинейных поверхностей или неоднородных конструкций с помощью 3D-сканирования или измерения по изображению.
2.Контроль Качества Поверхности
Внешний Контроль:
Визуально осматривать либо с помощью линзы или микроскопа проверять наличие дефектов на поверхности, такие как царапины, cracks, окисление, ржавчина, бurrs, впадины и т. д.
Проверять, является ли эффект поверхностных обработок (например, полировка, электроroplатирование, пескоструйка и т. д.) однородным.
Контроль Шероховатости Поверхности:
Использовать прибор для измерения шероховатости поверхности (например, стилийный или оптический) для измерения значений шероховатости поверхности (Ra, Rz и т. д.), чтобы обеспечить соответствие техническим требованиям.
3.Контроль Свойств Материала
Тест на Твердость:
Использовать твердомер Роквелла (HRB, HRC), твердомер Виккера или твердомер Бринеля для проверки соответствия твердости нержавеющей стали стандартам.
Анализ Химического Состава:
Использовать спектрометр (например, рентгенофлуоресцентный спектрометр, спектрометр прямого считывания) или метод химического анализа для проверки соответствия состава нержавеющей стали (например, содержания хрома, никеля, молибдена) требованиям маркировки.
Тест на Méханические Свойства:
Проверять механические свойства нержавеющей стали, такие как прочность и靭кость, с помощью растяжительных испытаний, испытаний на удар и т. д.
4.Контроль Внутренних Дефектов
Недestructive Testing (NDT): Недestroying contrôle
Ультразвуковая проверка: Используется для обнаружения внутренних дефектов, таких как cracks, поры, включения и т. д., и применима для деталей с толстой стенкой.
Рентгенографическое исследование: Обнаружать внутренние структурные дефекты (например, качество сварки, дефекты литья) путем создания изображения при прохождении рентгеновских лучей через детали.
Магнитнопорошковая проверка: Для ферромагнитной нержавеющей стали определять cracks на поверхности и вблизи поверхности.
П penetрантная проверка: Используется для обнаружения поверхностных открытых дефектов (таких как cracks, пористость) у непорösen материалов.
5.Функциональное Тестирование
Тест на герметичность:
Для деталей с герметичными требованиями (например, клапаны, трубные соединения) проводить гидравлические или пневматические испытания на давление для проверки наличия утечек.
Тест на Коррозийную устойчивость:
Проверять коррозийную устойчивость нержавеющей стали в конкретных средах с помощью испытаний в солевом распыле, испытаний на межзернистую коррозию и т. д.
Тест на Сборку:
Проверять, proceeds ли сборка и фиттинг деталей с другими компонентами гладко, чтобы обеспечить нормальную функциональность.